
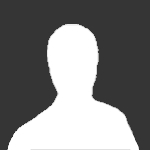
kab-pro
Members-
Posts
348 -
Joined
-
Last visited
-
Days Won
20
Content Type
Profiles
Forums
Calendar
Everything posted by kab-pro
-
Husqvarna 2004er DOHC 510ccm >> Motorrevision<<
kab-pro replied to dr.-hasenbein's topic in Supermoto Projektbikes
Cool DIY stopper -
You are speaking about this and this but not saying what next. I feel big changes is coming
-
DALI!!! what you will going to do??
-
Brunhild 5.0 der Name ist Programm
kab-pro replied to Joar-is-so1987's topic in Supermoto Projektbikes
120 for it nothing critical if it doesn't ran at complete race mode. From pictures looks pretty well, but of course pictures time to time lies -
Brunhild 5.0 der Name ist Programm
kab-pro replied to Joar-is-so1987's topic in Supermoto Projektbikes
why are you going to dismantle it -
If I was an air filter, this is what I'd be seeing looking at the engine And finally, after blessing her with a bunch of holes in the side panels and getting rid of the airbox lid, she is ready for a test ride. Thanks to everyone who has been paying attention / giving valuable advice / cheering / saying good stuff. The actual dyno test is pending, not so easy to schedule it. When it is available I will make sure to post the results but the build is done for now, but she will get even more upgrades as the next season comes! Stay in touch.
-
Continuing on the assembly, first to measure the required shim thicknesses. Setting the adjustable APE cam gear to 0 deg advance. To make sure of the valve-to-piston clearance we are using a mechanical and rather simple method. Clearance passed! And engine complete.
-
Custom camshaft from WebCam - third greatest investment from "cashflow" standpoint. I have to admit the existing (modified OEM) cam profile is very good which is only further supported by the simulations, but we shall replace it anyways because of the following reasons. - as explained previously, the aggressive lobes posess noteworthy self-destructing properties (they wear out very fast). This is probably because the hard layer of the lobes was grinded away. The consequences were clearly visible. - The aggressive profile is very hard on the valves and rockers, decreasing the life span of seats, guides and retainers. - Great risk of valve float at higher RPMs. - The dyno curve must be suited for supermoto, producing linear pull that peaks almost at the top of RPM range. By using the simulation data we chose the valve lift, duration and centerlines to reach the desired goal. We then had to choose from a list of available WebCams grinds to find the closest match and specify the centerlines. If we were to order our own grind, the costs would double. Props to Laurie@webcamshafts.com, the communication was excellent! To be honest, this is not the most powerful cam at all, there are a lot more grinds that require larger diameter followers and due to the massive overlap will be hard to start and idle. The costs will of course skyrocket for setups like those. But the cam we order shall combine the best from all worlds - easy starting, fair idle, not the best but very great power up top. We also order 2008 style cam gear with slots to mess around with retard/advance if needed.
-
Sorry for the hold-back guys. Continuing on the assembly! The second major investment - Xceldyne valvetrain: - single-piece titanium valves - titanium retainers - heavy-duty valvesprings - berillium-copper valveseats - bronze valveguides Why Xceldayne? - Brilliant lifespan / weight proportion. This becomes critical for those who plan on keeping the engine in the upper rev range. - Excellent thermal conductivity - Minimal wear. Xceldyne does not fail even after lapping the valves. Valve lash is practically frozen in time. Except for cases where oil changes have been skipped. We have used this setup on 2008 CRF and have never adjusted the valve lash or discovered any abnormalities in the valvetrain that would soon indicate the end of it. A few weight comparisons:
-
Right side assembling just wonted for me. Winter is coming u can do it again
-
A sneak-peek into the treasure chest. Engine assembly: The hour-meter was indicating 68 hrs before the great dismembering. Even though it was clear what we had the engine go through, we did not have the slightest idea if the previous owner had agreed with our opinion on correct usage and maintenance so we are better off installing everything new. Buying the internals in both OEM and AEM definitions in USA.
-
Competition, competition... There are two candidates to weld this stuff together. Candidate A: Candidate B: I guess we shall use option B. Taking thermal deformation into account, we had to deliver the bike at the workshop to fit together three segmented blocks. And finally, general view of a completed header. Big thanks to the guy who pulled it off - Igor.
-
And so, before welding the thing together, one last thing thats left is the head flange. Cranking up the big old CNC for that. Operation welding. Though it was initially considered to provide the least amount of problems, turns out everything else was a whole lot easier. Except welding. Initially we had our eyes on a true TIG master but to our disappointment, it was not possible to organize the process. Anyway, props to his test-seams. The best we have seen. We have to look elsewhere for an experienced TIG welder.
-
And a good morning here as well Dr. Hasenbein! Throttle_Jockey, the reason for this header was a bit different. That is why I posted those simulated dyno graphs, they show a great increase in horsepower levels if a shorter, tapered header is used in stead of the HGS. Periphery of the engine is also important, of course, otherwise I would have just built a header out of plumbing accessory..
-
The laser cutter has done it's job leaving only minor melt-spots which will be corrected manually. Two sets have been cut so that one of them can be fed to the hogs right away without too much regret. Rolling the freshly cut flat-patterns. Every segment must be catch-welded and rolled twice in order to obtain a near-perfect round shape. Rolling them only once will provide an egg-shape but that is enough for the catch-weld operation. Grinding away the melt-spots of the laser cutter and checking for compatibility between individual segment couples. Scotchweld. HGS vs unwelded DIY.
-
Lets start with the header extremes. Unfortunatelly there was no thick-wall tube available from stainless steel, so we had to buy a round bar and simply cut away the inner portion.
-
And so step by step, we have finaly reached a satisfactory result. The length is about OK and radius bends are all going where they should be. Conclusion - to decrease the amount of paper modles necessary for this task, the whole surrounding area of the motorcycle should be scanned. We shall return to this later. The materialization process of the piece of paper shall continue.
-
Project header: Unfortunatelly since the market does not offer a header with our desired length and taper, we shall build our own. There are of course guys like Ivan Lazzarini that somehow have the priviledge to order something that doesn't exist but that is another story. First, and we are already used to it, lets scan the HGS product. The main idea is to fix the entrance and exit in space, so that the rest can be changed. The new header must be a uniform taper from the beginning to the end. That defines the necessity to fashion it from sheet metal. The biggest challange is to route it around the frame and under the left radiator while avoiding the coolant lines. 3D model in progress... Fashioning a paper model using 1:1 scale print of the flat-patterns and using a glue gun to stick it all together. The idea is to evaluate how well the above mentioned has been accomplished. And if... Obviously there had to be a better way... And so a paper model after a paper model... Eventually, a result is reached, but it took 8-9 paper models to finally route the middle section of the header around all the obstacles.
-
As of now, we are moving closer and closer to the point where further increase of power demands additional engine capacity. Since doing that is out of the question for now, these two new curves represent the addition of a new, shorter exhaust header and a custom "webcams" camshaft, designed not only for brilliant top end power, but also very reasonable engine life, solid idle, and easy starting, without the necessity to run larger diameter followers. Two new curves: - Blue: CNC head + modified camshaft + shorter exhaust header - Yellow - CNC head + custom "webcams" camshaft + shorter exhaust header
-
Update: some new curves have been generated. - blue curve: OEM engine equipped with the CNC head - black curve: CNC head + HGS exhaust system + modified camshaft of unknown origin (found in my engine as bought). Both cases provide an improvement, most noteworthy when modifying the other gas exchange components.
-
Since now it is clear that this method works quite well and the stock baseline is ready, we can start figuring out what advantages are introduced with every upgrade. First off, the manually ported cylinder head. You can see that it alone backfires in +11% of power. The highest curve is the condition of the bike as we received it, featuring manually ported head, reground cam and full HGS exhaust system. Backfire screen removed. Result = +15% of power with noteworthy increase in the high end of revs.
-
When the head flow and cam profiles have been properly analyzed, we are finally ready to build a full mathematical model of the given engine. There are some powerful tools out there designed specifically for this task. They require a whole lot of different specs and evaluating those properly is the key to successfully generating a valid dyno graph. The most basic specs include bore, stroke, rod length and some of the more advanced specs include valvespring rate tables, head flow tables, cam files etc. When the graph has been generated, it has to be compared to another valid source. Since we didn't make any runs by ourselves, there is a site called MotoUSA with plenty of different dyno sheets. Here is the comparison between what they have published and we have generated using ONLY a mathematical model. 2013 CRF450R stock You can see the resemblence being quite believable. The slight differences that you are seeing are due to fuel mixture, spark curve and environmental conditions. And of course the allmighty error of math regarding such complex things, which to my surprise, is proving to be somewhat unimportant, since the goal of this virtual simulation is to evaluate the changes brought from every mod, not reaching absolute numbers.
-
Yes, that is beryllium bronze. It has proven to last forever when used together with titanium valves. That is actually a full Xceldyne valvetrain kit. A bulletproof setup. About the surface roughness - I have left it as you see in the pictures. No smoothing. Smooth surfaces condensate and accumulate fuel droplets essentially ruining the mixture. Thus, it has been proven that the best aero and hydro-dynamic properties have been displayed by surfaces that are not smooth, for example a golf ball or shark skin. That is why I have left the surface wavy and textured. Simply out of curiosity.